ARTICLE DATE: October 2000
The roots of the CC program are planted firmly in the homebuilding community. The first aircraft Jay helped his father build was a one-person autogyro. The CC gyroplane prototype is essentially a high-technology autogyro.
More precisely, it is a modem, 5-place fiberglass and carbon composite fixed-wing airplane with a high-inertia rotor. All systems were designed for simplicity and ease of maintenance. Due to the unusual nature of the CC, it enjoys support from both rotorcraft and fixed-wing homebuilders, offering something unique for both camps I know of no other air craft that can claim this. (All Performance Values Are Based on Standard Engineering Principles, Reasonable Drag Coefficients and CC Gyroplane Prototype Flight Test Data Collected To Date.)
Eight months have elapsed since the CC accident last December. The CC was not only rebuilt during this time, but was improved with numerous design changes that came from 15 months of intermittent flight testing before the accident. The first step is for the rebuilt CC to do high speed taxi tests at Sheppard AFB in Wichita Falls, Texas.
If everything looks good during the taxi tests, the CC will be flying again before the end of August. Check the CarterCopter website (https://carteraero.com/) for the most recent update on its progress.
By now, most people who follow the CC program understand that the current CC gyroplane prototype is a test platform, not a production vehicle. It was created to prove design concepts for a new class of zero-roll takeoff/landing rotorcraft.
The CC prototype is attempting to combine the inherent safety features and simplicity of the autogyro with the efficient, high transit speeds of a fixed-wing airplane. Once the design concepts are proven, they can be used to create an almost infinite variety of CC aircraft.
The CC gyroplane design software system has specific design capabilities and limitations. You can max one of the following at the expense of the other three:
Range: 26,000 miles range (airborne for “four-plus” days with out refueling).
Speed: 500-MPH (limited by a rotor advancing tip-speed of 600-MPH).
Altitude: 70,000 feet.
Useful load: 100-150 passengers/equivalent cargo.
By comparison, the CC prototype is designed for a range of 2400 miles with a 45-minute reserve. It should cruise at 220 MPH @ sea level and 350 MPH TAS @ 45,000 feet altitude. Empty weight is 2500 lbs with gross weight VTOL of 4200 lbs (STOL of 5000 lbs).
A production version of the same aircraft should weigh 2200 lbs. The actual performance for any future CC design (homebuilt or commercial) will be determined by the following choices:
Rotor: its diameter and solidity (blade area to swept area).
Wings: the span and area.
Engine(s): HP, type, and number. If propeller driven – include prop efficiency.
Fuselage: volume, pressurization, and coefficient of drag for the wetted area.
Functionality: gyroplane or Heliplane (helicopter + gyroplane) capabilities.

Ground testing of the Carter Copter’s power systems. Engine covers off in this picture.
The CC Heliplane is a recent design derivative of the CC gyro plane. More details about the Heliplane can be found on the CC website. Basically, it is a CC gyro plane with the added benefit of full helicopter capability for takeoff, hover (including sling loading) and landing.
The Heliplane, like the CC gyroplane, is a design concept that can be built in an endless variety of sizes, weight categories and degrees of sophistication.
With sufficient empirical data, a software program can be written to design a CC with maximum capabilities for any specific job – whether it is a relatively inexpensive, and non-pressurized homebuilt, or a “loaded” military version designed for combat.
CarterCopters, L.L.C, is developing such a program. Numerous components found on the CC prototype have application on other aircraft – both rotor craft and fixed-wing:
Landing gear: will absorb 20 feet per second sink rates with no damage – using an 18 inch stroke. The gear will absorb 25 fps sink rates with only moderate damage. The accident last December proved the gear’s merit.
An upgrade of the current system planned for the CC Heliplane, which includes a much longer stroke, would permit 50 fps sink rates with no damage. The upgrade includes use of a new type of hydraulic fluid that provides a variable viscosity controlled by electrical input.
Propeller: light weight (low inertia) and high efficiency. It can be used equally as well in either the tractor or pusher configuration. Tests show it should prove to be 90-94% efficient. Reverse pitch can be provided.
Prop controller: fully automatic, computer controlled, variable pitch. It is designed to maintain maximum prop efficiency under a wide range of speeds, power settings and altitudes (useable on both piston and propjet aircraft).
In the CC Heliplane, the prop controller is used to provide counter-torque control during flight in helicopter mode that is invisible to the pilot.
Rotor head control system: lightweight and simple. It contains no swash-plate or blade pitch bearings. It provides a lightweight, simple method of changing the rotor plane of rotation (cyclic control). The CC gyroplane has no rotor gear box (heavy and high-maintenance) as found on helicopters and tilt rotors.
The CC Heliplane has a rotor gearbox that can be much lighter and less expensive than a helicopter’s since it is used only during the brief periods spent flying in helicopter mode (takeoffs, slow flight, hovering and landings).
Pressurized cabin: designed for 40 PSI and tested to 25 PSI. It utilizes a one-fourth (¼) inch-thick, stretched-acrylic windshield (bird strike resistant) and a lightweight, simple, pressurized fuselage door.
The components listed above are currently unique to the CC gyro plane prototype and the Heliplane design, but are NOT what makes CC aircraft uniquely different from other rotorcraft.
HEART OF THE CARTER COPTER
What makes the CC design revolutionary is its ability to keep the rotor stable at advance ratios “mp” greater than “one” (mµ>1: aircraft forward speed greater than the rotor tip speed). This one concept provides CC aircraft with the unique ability to do two very important things that other rotorcraft can not do.
Maintain rotor stability at high forward speeds and low rotor RPM (very high mp advance ratios). At speeds above 125 MPH, the CC prototype’s rotor has zero pitch. Above 200 MPH, the rotor disk is almost flat to the relative wind – which almost totally unloads the rotor.
When not producing significant lift – the rotor slows to 75-90 RPM. Even at this slow tip-speed, the centrifugal force (C.F.) created by the weighted rotor-tips keeps the rotor blades stiff (similar to spinning a 65 lb rock at the end of a 2174 foot rope).
This rotor “stiffness” at low RPM prevents the relative wind at high forward speeds from lifting and snapping-off the blades. Rotor stability and lift equilibrium between the advancing and the retreating blades are assured by unloading the rotor so that it is not producing any thrust and very little lift — and by allowing the rotor to teeter at the rotor head.
Fly as fast and efficiently as a fixed wing aircraft using the same size engine. Again, the key is being able to slow the rotor down to 75-90 RPM when flying at high for ward speeds. This reduces the rotational aspect of the rotor profile HP to approximately 1/27 of the rotational profile HP @ 270 RPM – the rotor speed used during slow flight.
Since the wings are not used for takeoffs and landings, they can be designed with low profile drag (small wing area for a given gross weight) and low induced drag (high aspect ratio wing) to be very efficient at high forward speeds and high altitudes. The combination of low rotational drag on the rotor plus low profile and low induced drag on the wings produces a fast and efficient aircraft.
The CC high-inertia rotor provides a number of other benefits as well:
Zero-roll takeoff: The 65 lbs of depleted uranium* in each rotor tip create a “flywheel” that stores large amounts of energy. Brakes are locked and the high-inertia rotor is pre-rotated to 425 RPM using power from the engine. The rotor is then disconnected (freewheels) and the engine brought to full power before collective is pulled.
When collective is pulled, the resulting rotor-pitch converts the stored energy to downward thrust sufficient to produce a jump takeoff. *NOTE: Sintering tungsten carbide (as used in cutting tools) will be used in CC production aircraft in place of depleted uranium. The two materials have similar specific gravities.
Landing with 4-5 seconds of hover on a dead engine: Because the high-inertia rotor is always in auto-rotation, altitude energy is easily converted to rotor “flywheel” energy through an overspeed in rotor RPM. The “flywheel” energy can be stored even when the engine has stopped.
The stored energy will provide 4-5 seconds of hover when collective is pulled in landing – or enable the pilot to stop his descent and climb upwards for a second landing attempt at a different spot. The high-inertia rotor also provides gyroscopic stability in turbulent air at flight speeds as low as 30 MPH – and will help to smooth landings in such conditions.
NASA continues to help fund our R&D program though a SBIR Phase III grant. They established five goals they wish the CC to accomplish:
-
Zero roll takeoff.
-
Zero roll landing.
-
Fly above 10,000 feet altitude.
-
Fly 600 miles without refueling.
-
Fly at 150+ MPH at a mp greater than 0.8 in steady state flight.
Achieving these five goals will be our primary objective once flight testing resumes.
Rod Anderson is a shareholder in CarterCopters, L.L.C, and reserved the production slots for the #1 CC kit prop and the #1 CC kit jet. As an unpaid volunteer with a vested interest, he helps the small crew that Jay Carter heads (never more than 12 people) with paperwork and public relations “to free Jay for the more important things — like getting the CarterCopter back into the air and keeping it flying”. Rod has done so for the past 28 months. He would like to hear your ideas, suggestions and questions regarding the production of CarterCopter kits.
CarterCopter High-technology
Structure:
-
Seamless molded composite.
Cabin:
-
Occupants – five (2 in front, 3 in rear bench seat).
-
Windshield is 1/4-inch thick acrylic (bird strike resistant).
-
Pressure differential – 10 lbs / sq inch (proof tested to 25 psi).
-
Voice audio alarm system for flight safety.
Wings:
-
Span – 32 ft. Area – 77 sq ft.
-
Flaps & ailerons are combined.
-
Wing sections outboard of tail booms are removable.
-
Width of aircraft with wings removed – 8½ ft (necessary for highway transport by trailer).
Tail Booms:
-
Extend below the prop tip so prop is protected in a wheels-up landing.
Tail:
-
Large tail volume for excellent directional stability and safety considerations under certain flight conditions.
-
Stabilizer – 100% moveable. 2½ ft extensions outside of vertical stabilizers are removable for highway transport by trailer.
Rotor (bearingless):
-
Diameter-43.5 ft. (10 ft addition added 01/06/00).
-
Weight – 274 lbs, less than 11% of the aircraft’s empty weight (includes 130 lbs L.E. weights, rotor hub and blade pitch horn). Carbon composite construction with twistable carbon spar.
-
**Airfoil is 7-in wide at the tip and 17-in wide at the root. Unique design for flight at mµ>1.
-
Leading edge tip-weights – 65 lbs in each blade. Inertia from weights allows the aircraft @ 3500 lbs to take off vertically and clear a 50 ft obstacle 75 ft away. Weights are currently made from depleted uranium but in production will be made from sintering tungsten carbide.
Prop (bearingless) (shown in high-speed cruise on 3-View AutoCAD drawing):
-
Diameter – 96 inches (2-inch addition added 01/06/00).
-
Weight – less than 30 lbs (includes pitch change mechanism).
-
Carbon composite construction with twistable carbon spar.
-
Chord is 21-inches at the 25% radius and 8-inches at the 75% radius.
-
Thrust centerline is through the aircraft’s average center of gravity for safety considerations.
Engine – Corvette LSI with 2 turbos in series:
-
600 HP for short duration from 0-30K ft altitude.
-
300 HP at 45k ft altitude.
Landing Gear — air over hydraulic:
-
Main gear retracts into the tail booms.
-
18-inch stroke can absorb a 20 feet per second impact.
Fuel — 160 gal total:
-
Fuselage – 60 gal.
-
Center wing section (under fuselage).
-
Outboard wing sections – 25 gal each side.
Cruise Speed @300 HP:
-
220 MPH @ sea level.
-
350 MPH @ 45,000 ft.
Range:
-
2400 miles with 45 min reserve.
Empty Weight:
-
Prototype – 2500 lbs.
-
Production – 2200 lbs (estimated).
Gross Weight:
-
VTOL-4200 lbs.
-
STOL-5000 lbs.
*Patented
** Patent Applied For*
Safety Through Education – Pilot Training
by Kerry Cartier, the PRA Safety Guy
Gyro Crash Score: Trees 1, Gyro 0, and a Penalty Time-Out for the Pilot
Chopper Charlie made a point of visiting his buddy, Claude Al-Deway, in the hospital after Claude crashed his open-frame, single-place gyro in the trees. “Hey, Claude, how do you feel?” Charlie asked.
“Pretty good,” said Claude. He didn’t look pretty good. In fact, he looked pretty awful, with his head all bandaged up and his arm in a cast. “I guess I really some stupid things,” he said.
“I reckon you’ve told the story before, but tell me what happened,” Chopper Charlie said. “Maybe I’ll get the PRA Safety Guy to write a story about it. Your name in lights, and all that…”
“Well, I was flying pretty low across the meadow, not watching what I was doing, and all of a sudden there were all these trees!” Claude said. “I mean, it was like they jumped out of the ground so they could grab my gyro!”
“You’re kidding!” Chopper Charlie exclaimed. “Did the trees really try to grab your gyro? Or did it just feel that way?” Here was a chance to check if Claude had mental problems, in addition to his obvious physical ones.
“It just felt that way, Charlie. That’s when I did something stupid,” he said. “Instead of aiming at the base of the trees, giving the engine full power, gaining airspeed, then jumping the trees – why, I gave it full power and pulled back on the stick instead.”
“Uh-oh! If you had an airplane, that might have worked. But with a gyro…” Chopper Charlie said.
“… Yeah, yeah, I know, with a gyro that was exactly the wrong thing to do. It almost worked, Charlie. I actually got over the top of the trees,” Claude said. “But there wasn’t enough airspeed, and with the stick back in my stomach and the engine roaring, my gyro dropped right into the tops of the trees!”
“That must have hurt!” Charlie said, in a consoling tone. “What happened next?”
“I’m not really sure,” Claude said. “But when I finally got my wits about me, the gyro was in the treetops, hanging from the remains of the rotor blades, the engine was off, and I was maybe 50 feet above the ground.”
“My gosh, you were lucky!” Chopper Charlie said. “How did you get down?”
“Well, I was belted into the pilot’s seat, so I felt safe. My legs were lacerated from dropping into the trees, and so were my arms. But at that point nothing was broken,” Claude said. “That’s when I made my second stupid mistake.”
“Another stupid mistake? Come on, Claude, you’re being too hard on yourself,” Chopper Charlie said.
“No, no, it really was stupid. You see, there was this big branch almost within reach of my left arm. I figured that if I could reach it, I could climb down the tree. So I reached for it, I grabbed it, and I pulled real hard on it so I could get closer to it,” Claude said. “Then it happened!”
“All of a sudden, the gyro tilted to the right, and I lost my grip on the branch. The gyro turned bot tom-side up and plunged down through the trees another 30 or 40 feet. When it stopped, I was hanging bottom-side up in the cockpit, about 8 feet above the ground,” Claude said. “I was just hanging there, Charlie. I figured the gyro was done falling through the trees, and I was still alive, and every thing had turned out okay.”
“That is a truly amazing story!” Chopper Charlie said. “Wow!”
“Then I did something really, really stupid,” Claude said. “I unfastened my seat belt.”
Pre-fright Inspections and Safety Why-ers
There I was at 500 feet, flying happily along, when I heard a loud BANG!!! and looked back at the cloud of splinters that used to be my propeller.
“Uh-oh,” I said. (This story has been edited for PG audiences.) “Double uh-oh, even!”
I killed the engine (which was trying to kill itself), put the nose down to keep the airspeed up, and looked for a place to land. There it was, right by my ankles, the perfect place! And immediately thereafter, I had the perfect landing. (A landing is good if you can walk away from it. A landing is perfect if you can run away.)
After my knees got out of automatic-shiver mode, I checked my emergency kit for the spare Pampers and handi-wipes. Then I checked the aircraft. Obviously something had gone through the prop. (I, too, have flashes of genius on occasion!). In another flash of genius, I decided that the cause was NOT termites.
What was it? There were several possibilities, but the hole where an engine mount bolt used to be seemed the best choice. No way to be sure, of course, because that bolt was missing. But so was half the prop.
Hmmm. Did my preflight checklist include checking motor mount bolts? I had used it just a couple weeks ago, and I had stashed it —I mean carefully put it away — under the seat cushion.
Osmosis, you know… sit on something long enough and you absorb all its knowledge.
Motor mount bolts were not on my preflight checklist. I carefully wrote that in, as soon as my hand quit shaking. Other write-ins include muffler springs, radiator cap, air filter, reduction drive drain plug, and even the reduction drive filler cap (a little plastic thing that can cause more damage than you’d believe).
There’s a tale or two about these write-ins, but I won’t tell it here. All I’ll say is that a preflight checklist is not written in concrete. The items on a preflight checklist expand, based on your actual experience with the aircraft. (And that’s ALL I’ll say!)
Well, we got the machine home in the back of a truck. Then I phoned the propeller manufacturer. “Hey, I’ve just had a little problem,” I said.
“Kerry Cartier? Is that you? I thought I recognized your voice again,” he said. “Say, your special discount is still good if you buy two wooden props at once. And just for you, I’ll throw in a roll of safety wire.”
I bought the props, again. When they and the safety wire came, there was a note: “Safety-wire everything that could fall through the prop.” So, in addition to the write-ins on my preflight checklist, I safety-wired the engine oil drain plug, the fuel filter, the fuel pump, hose clamps on the radiator hoses, the trim spring, and the carburetors.
I also safety-wired the biggest thing that could fall through the prop, the large nut behind the control stick.
Good thing I have a laptop computer, or you wouldn’t be reading this.
“Preventive Maintenance Prevents An Engine Failure”
By Dave Geboy, PRA Chapter 18
At Sun ‘n Fun this year, a friend suggested I replace the car buretor sockets on my Air Command 532. They tend to crack with age, leaning the fuel mixture and causing engine failure.
These carburetor sockets — the rubber sockets between carbu retor and intake manifold — cost over $40 each.
When I replaced them, I found a bigger problem. There’s a bead of rubber inside the carburetor side of the socket to ensure a tight fit on the carburetor. The top half of the bead was gone, probably caused by a loose clamp on the car buretor socket.
Carburetors and air filters vibrate in flight, so I safety-wired them to the Rotax 532 engine so they can’t fall off.
On aircraft, you “anticipate” failure, based on the experience of others, and replace parts “before” they fail.
Preventive maintenance is cheap insurance. I was only hours away from losing that carburetor.
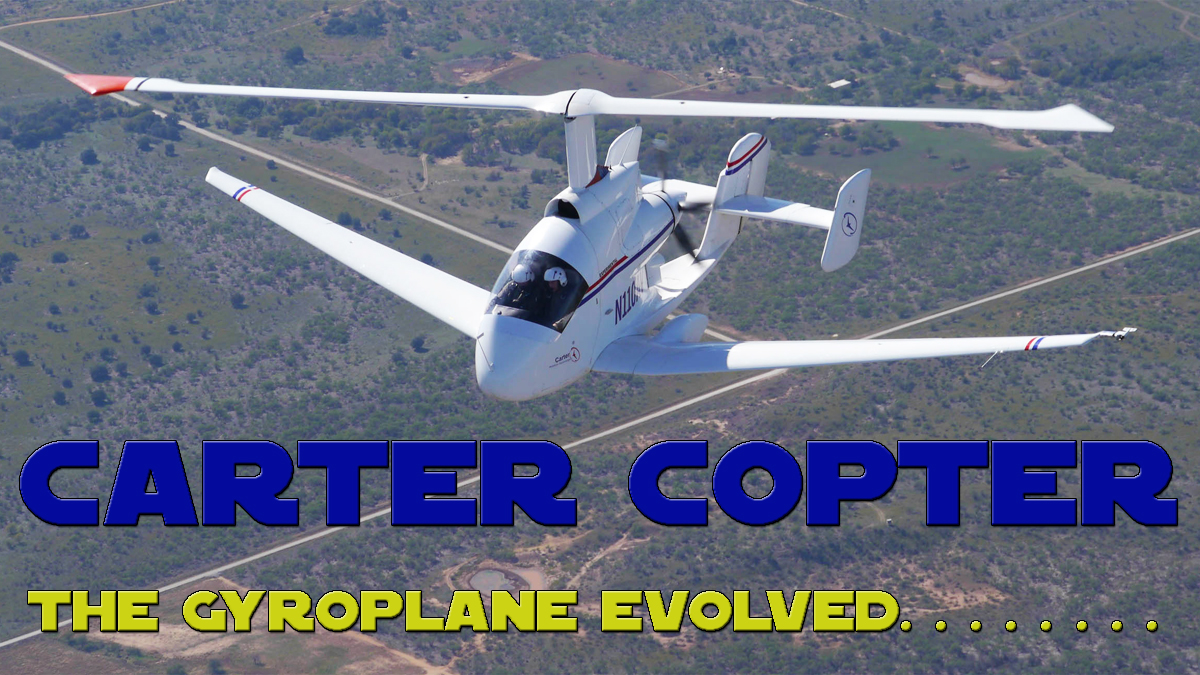
It’s an incredible aircraft! I like it very much.